CSR HEBEL POWER FLOOR PANEL TONGUE & GROOVED (T&G) 1800 x 600 x 75mm
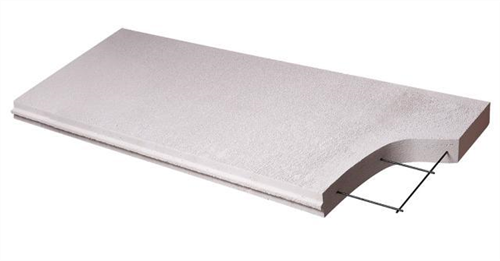
AUTOCLAVED AERATED CONCRETE (AAC) PANEL TONGUE & GROOVED
ONE AAC FLOOR SYSTEMS DESIGN AND INSTALLATION
Floor systems at one AAC are designed to be used in every residential or commercial construction projects with qualities like solid, masonry and lightweight, high fire resistance, and sound acoustic qualities. For fast and clean construction procedures our Floor Systems are available in standard sizes of 2200mm in length and 600mm in width. A level of quality is maintained in the project from the initial beginning to the completion of the project.
Quality floor panels by one ACC are installed by approved installers as per the floor systems design and installation manual. Moreover, there are a strict set of protocols that are followed by our team to offers a warranty of 15 years on materials and 7 years on workmanship adding peace of mind to all owners of the construction project.
Loxo reinforced AAC floor systems are preferred to be used in residential construction over timber or steel framing floor joists systems spaced at 440mm centres. Loxo and associated manufacturers both adhere to the ISO 9001 international standards for management of quality at its best. The 50mm thick, steel reinforced loxo floor panels are manufactured from autoclaved aerated concrete with an average density of 560kg/m³.
The loxo floor panels are supplied in standard sizes of 2200mm in length and 600mm width and have an average weight of approx 37kg/panel. For the installation of a 50mm loxo floor systems tools like power drills, drive bits, cordless drills, power saw with diamond blades, vacuum, mixing drill, mixing bucket, electric leads and power box are needed. Download PDF available on our website to get into details. Loxo floor systems are flat-packed in a pack of 20 and delivered to site with approved lifting devices. We take all care to avoid damage to the face, ends and edges of the panels. Physical manual handling of floor systems are kept at a minimum, we use trolleys and/or other mechanical devices for delivery of panels.
Health & safety are maintained with respect to loxo floor systems however when cutting, drilling, sawing, routing, chasing, sanding and in any way breaking up the material there is the potential for health problems to occur for which standard precautionary measures are taken by one AAC under the occupational health and safety act.
WHAT IS AAC? (LIGHT WEIGHT CONCRETE)
Autoclaved Aerated Concrete (AAC) is manufactured from cement, sand (silica), lime and water, it is aerated by adding an expanding agent to the mix (small amounts of aluminum paste). The mix is poured into a mold (a very large cake tin), to approximately 2/3 of the height of the mold, almost instantly the expanding agent reacts with the other elements, and the mix begins to rise in the mold. (A chemical reaction expands the mixture to form small, finely dispersed air bubbles).
The molds are pre-cured in a heated room for several hours. Then the semi -solid material (still in a green state) is transported to the cutting machine. The soft but semi-solid block is sliced into the required panel size using steel wires. Once sliced, the block is steam pressure cured in autoclaves for up to 12 hours. The expanding chemical reaction combined with the Autoclave process is what gives AAC it’s unique properties. AAC has excellent thermal insulation and acoustic absorption properties, it has superior fire resistance qualities and is also termite resistant.
Its properties and specification satisfy all relevant building codes. Working with AAC is easy and efficient. AAC is both versatile and economical. AAC meets the diverse demands better than any other material due to the numerous advantages of its physical and mechanical properties.
The Benefits of AAC Panel
Weight (KG) |
Click here to view the full Shipping Details and Returns Policy.